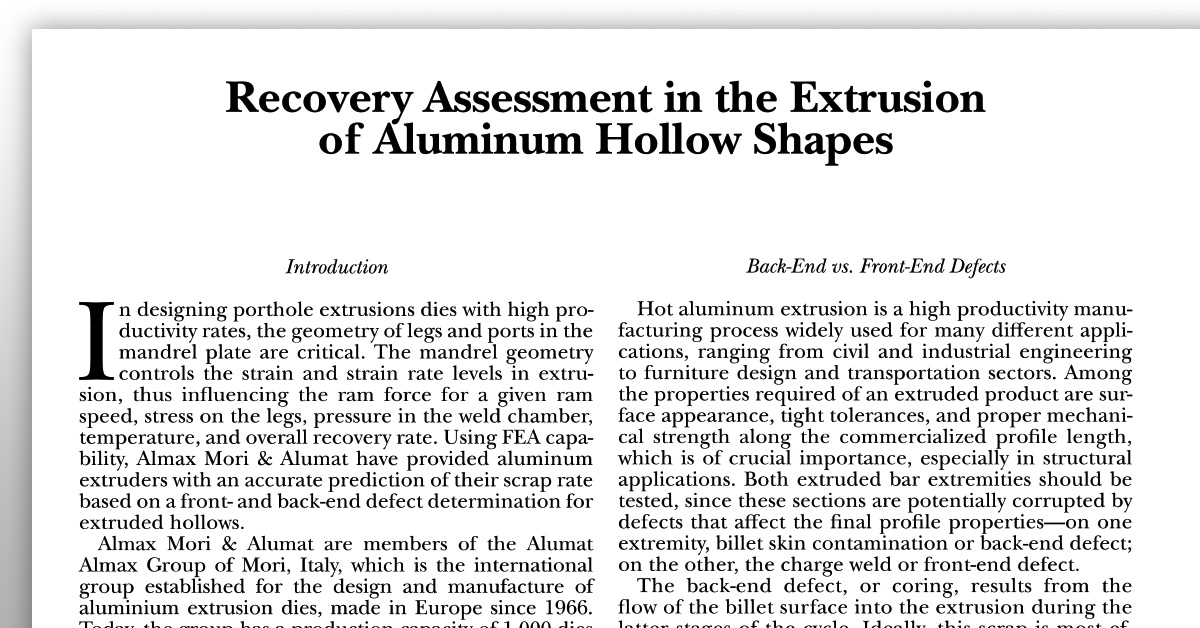
Recovery Assessment in the Extrusion of Aluminum Hollow Shapes
Abstract
In designing porthole extrusions dies with high productivity rates, the geometry of legs and ports in the mandrel plate are critical. The mandrel geometry controls the strain and strain rate levels in extrusion, thus influencing the ram force for a given ram speed, stress on the legs, pressure in the weld chamber, temperature, and overall recovery rate. Using FEA capability, Almax Mori & Alumat have provided aluminum extruders with an accurate prediction of their scrap rate based on a front- and back-end defect determination for extruded hollows. Almax Mori & Alumat are members of the Alumat Almax Group of Mori, Italy, which is the international group established for the design and manufacture of aluminium extrusion dies, made in Europe since 1966. Today, the group has a production capacity of 1,000 dies per month, made on specialized machining centers with integrated CAD-CAM systems.